Weighing Automation For Bulk Loading Of Cement
Existing Process
- Customers ask for the required quantity of cement to be filled in Bulker
- Cement plants weigh the empty truck and goes to the packing plant for direct filling of cement.
- In packing plant cement is loaded on to the bulker up to % capacity and asks the truck driver to go the weigh bridge to know the quantity of cement that has been filled.
- The above process is made several times and one point of time the cement that has been filled exceeds the required quantity.
- Further compressor has to be used to suck the cement back, still the exact quantity may not be obtained and requires excess cement to be sucked and the whole process is repeated until required quantity is loaded.
- This is a strenuous and laborious process to fill the target weight as required by the customer.
- Spillage of cement is more.
- Filling is at one point and weight ticket is issued at a different location.
- Filing process is not professional
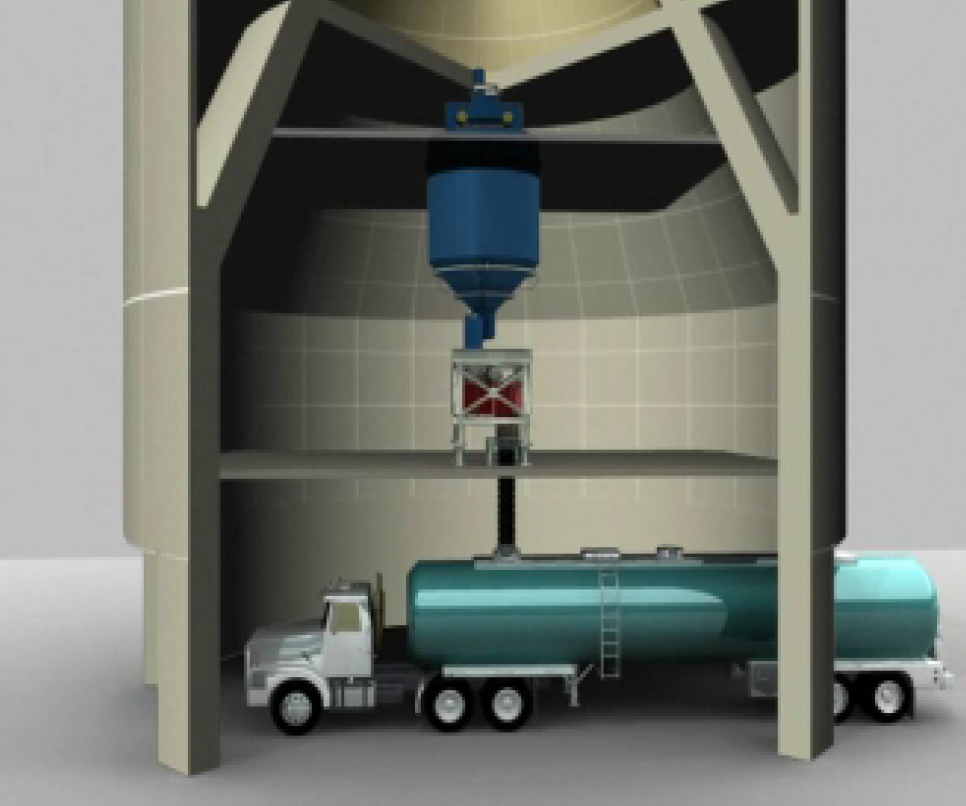
Problems Faced Due To The Above Process:
- Exact quantity of required cement could not be filled at one single shot.
- Un necessary movement of truck
- Fuel consumption is more
- Increased Loading time
- Higher traffic movement
- Truck retained for longer time
- Operator Productivity is reduced
- Man power required is more
- Compressor usage also adds to the power consumption.
- Excess filling of cement
- Spillage of cement
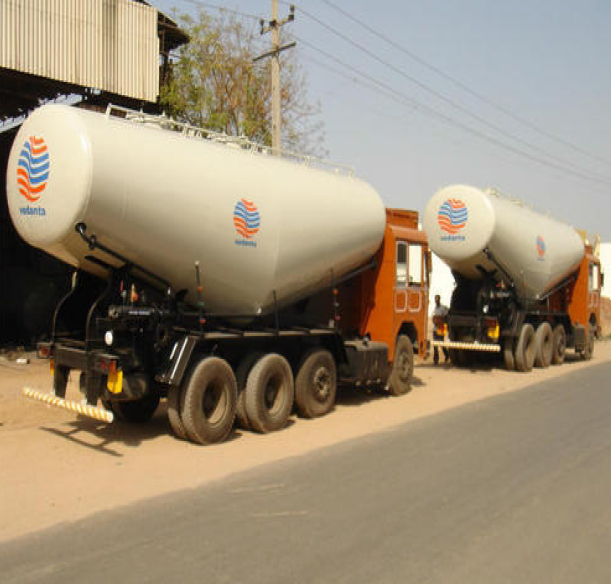
ANTARES WEIGHING solution for Bulk Loading of Cement
- Weigh bridge is installed underneath the filling chute.
- Truck weight will be Zeroed before the filling of cement starts
- Target weight required can be directly filled at one single shot
- Provide Suitable controller/ PLC control/ Automated software with complete protection.
- Provide suitable controls to operate different types of valves.
- Separate 4- 20mA output
- Dedicated Graphics Weight controller approved by Legal Metrology
- Software program to suit customers requirement
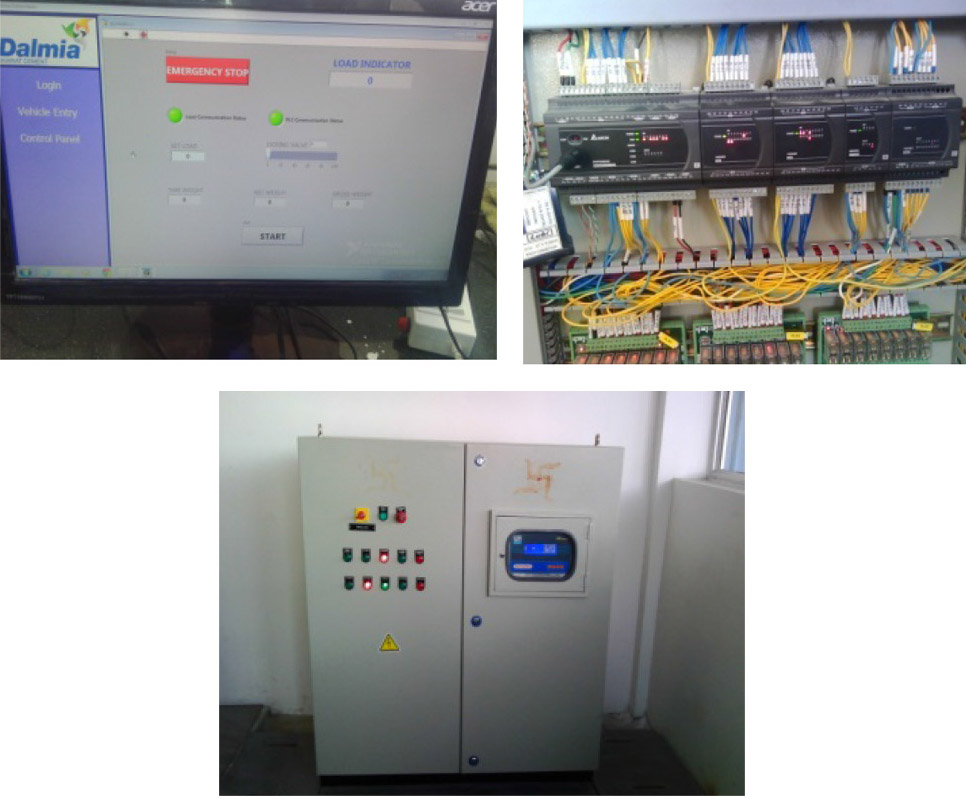
Advantages and Benefits to cement plant:
- Single weighment
- Proper alignment of Chute with Bulker filling mouth
- Filling area will be clean
- Movement of Trucks will be smooth
- Loading time is saved
- Operator time is saved
- Operator need not monitor the weight
- Weight ticket can be issued at the filling point itself
- Fuel saving
- Power on usage of compressor will be saved
- Compressor work is eliminated
- Additional High bright extra display provided for the truck driver to know the weight without entering into the weigh room
- Spillage of cement will be considerably reduced.
- Excess filling is avoided resulting in saving of money.
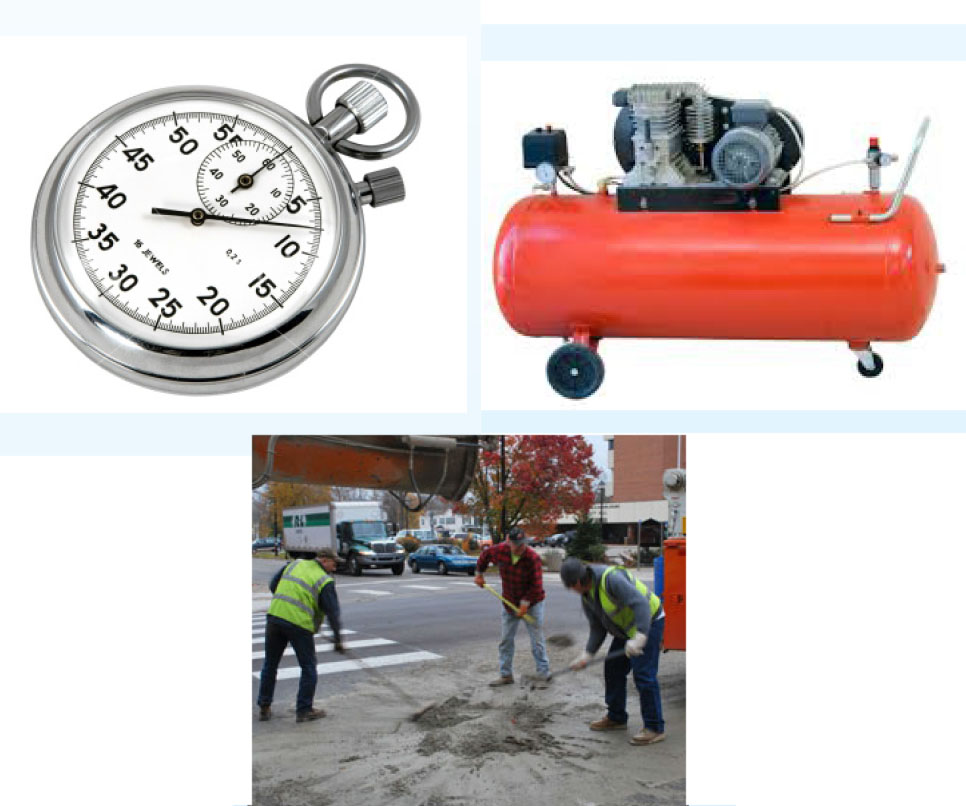
SAFETY PROTECTION
- Sensor fitted to ensure that filling starts only after truck is positioned on the platform.
- Software program is made such that the filling valve opens only with minimum truck weight feeded for safety.
- Signal post to ensure that truck driver leaves the platform after green signal only ie only after the complete filling is completed and chute is lifted up.
- Hooter also provided to inform the driver to leave the platform Emergency stop provided to stop the filling process in case of emergency.
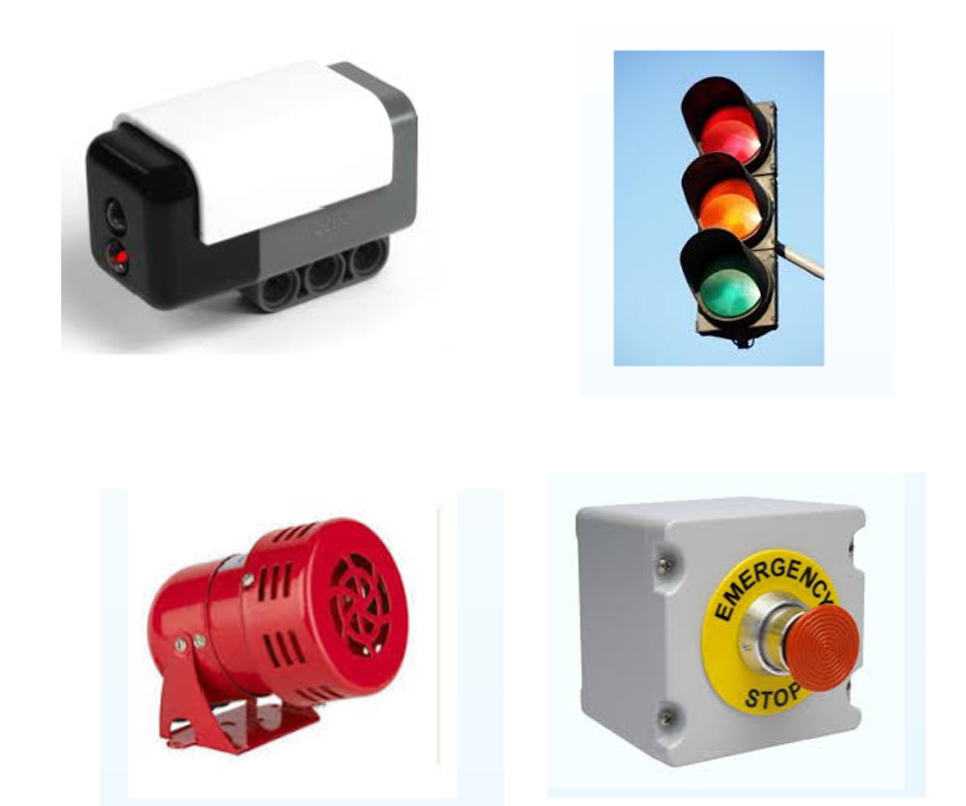